
How U.S. Tariffs Are Reshaping Construction Costs in 2025
U.S. tariffs on lumber, steel, aluminum, and more are raising construction costs across America. Discover how these trade policies are impacting homebuilders, commercial projects, and timelines in 2024–2025.
Why Builders and Developers Are Facing Their Most Expensive Year Yet
Introduction: The Tariff Squeeze Hits Construction
In 2025, U.S. builders are contending with an increasingly burdensome cost curve — and tariffs are a major culprit. Trade policies first introduced during the 2018 disputes have evolved into a broader, deeper set of tariffs on critical construction materials like Canadian lumber, imported steel, aluminum, and hundreds of finished goods. These tariffs are inflating material costs, delaying projects, and putting pressure on housing affordability and infrastructure investment alike.
This post explores how these tariffs are affecting both residential and commercial construction — from raw material prices to scheduling and labor — and what the industry is doing to adapt.
1. The Key Tariffs Driving Up Building Costs
Lumber: Canadian Softwood Tariffs Up to 40%
In 2024, tariffs rose from 8% to 14.5%, with a proposed increase up to 40% in early 2025 (now paused).
Canadian lumber accounts for nearly 85% of U.S. softwood lumber imports — making U.S. homebuilders especially vulnerable.
Steel: Section 232 Tariffs Return
A 25% tariff on all imported steel was reinstated in February 2025, eliminating prior exemptions.
Steel is vital in commercial and public projects — over 47% of U.S. steel use comes from construction.
Aluminum: Expanding Tariff Reach
A 10% tariff on aluminum imports remains, but has been expanded to cover nearly all sources.
Affects everything from HVAC systems to windows and siding.
China & Others: Finished Goods and Fixtures
10–25% tariffs on over 460 Chinese-made construction products (e.g. lighting, flooring, tools).
Proposed “reciprocal tariffs” could affect almost all imports, excluding Canada and Mexico.
2. Rising Costs: How Tariffs Ripple Through Construction
Material Prices Spike
Construction material costs have risen 34% since late 2020.
Lumber up 23.5% YoY in April 2025; rebar prices surged 26% after steel tariff reinstatement.
Housing Gets Pricier
Tariffs are adding $10,900 to the cost of a typical new single-family home.
Affordability suffers, especially for entry-level buyers.
Commercial & Infrastructure Hit Hard
Steel-intensive projects (e.g. warehouses, bridges) face large cost escalations.
Public projects see over-budget bids and delays.
3. Labor and Scheduling Impacts
Project Delays and Cancellations
68% of home builders report project delays due to material cost renegotiations.
Long lead times (14–18 weeks) for key materials like architectural metals.
Labor Market Volatility
Elevated costs threaten job growth in construction if projects slow or margins shrink.
Contractors can’t always pass costs to clients — hurting profitability.
Extended Timelines and Financing Pressure
Delays increase carrying costs and interest payments.
More builders using contingency budgets and early procurement to manage risks.
4. Residential vs. Commercial: Different Pressures
Category: Residential, Commercial. Key Material: Softwood lumber, Structural steel, aluminum. Tariff Impact: Adds ~$9K–$11K per home, Hundreds of thousands on large-scale builds. Cost Pass-through - price-sensitive buyers. Easier via lease rates, but ROI can suffer. Outlook: Slowing starts, lower builder confidence, Delayed project planning, sector-dependent
5. Industry Forecasts and Commentary
NAHB warns tariffs will worsen affordability; urges relief.
AGC & ABC caution about job losses and project cancellations if tariffs continue.
KPMG & Dodge Data expect 2025 cost inflation to outpace general inflation, with potential construction slowdowns in late 2025 if trade tensions escalate.
6. Mitigation Strategies: How Builders Are Adapting
✅ Strategic Sourcing
Shift to domestic lumber (e.g., Southern Yellow Pine) or alternate imports.
Apply for tariff exclusions or use foreign-trade zones.
✅ Forward Buying & Bulk Orders
Lock in material prices early or stockpile.
Cooperatives or buying groups help smaller builders reduce cost exposure.
✅ Design & Material Optimization
Redesign with less tariff-hit material (e.g., concrete over steel).
Use engineered wood or fiber-cement to avoid aluminum/lumber tariffs.
✅ Escalation Clauses & Financial Buffers
Contracts now include price clauses to protect builders.
Developers build in 10–15% contingency budgets.
✅ Policy Advocacy
NAHB and AGC lobbying to pause or repeal tariffs.
Legislative efforts underway to boost domestic supply and reduce import reliance.
7. Final Thoughts: What Comes Next for U.S. Construction?
Tariffs are acting as a stealth tax on builders, developers, and ultimately buyers. With steel, aluminum, and lumber duties at multi-year highs, the cost burden is significant — especially for affordable housing and large-scale commercial development.
Unless tariffs are lifted or counterbalanced with new trade agreements, many in the industry fear a pullback in construction activity just as demand for new housing and infrastructure peaks.
The path forward? Stay informed, advocate for smart policy, and plan projects with flexibility in mind.
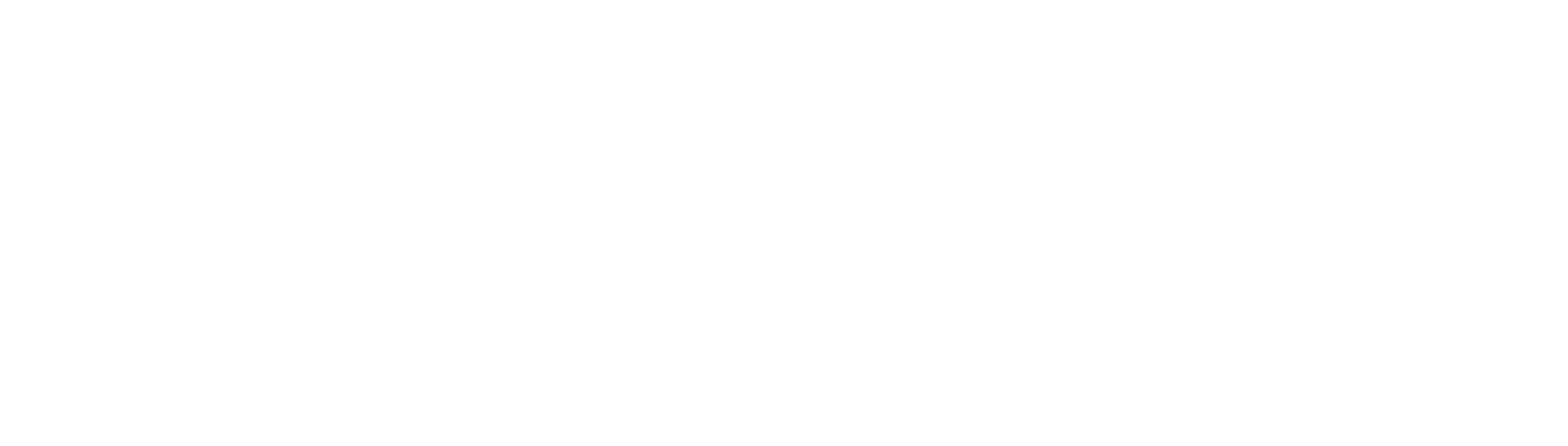
Stop Playing
Lets Get Busy